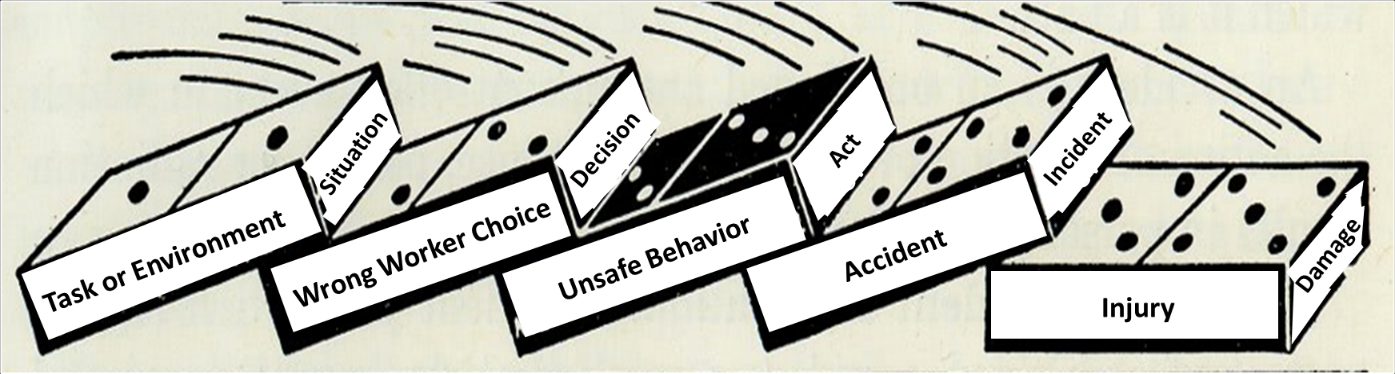
Many organizations believe that occupational accidents and
resulting injuries are caused by some short coming on the part of the
individual worker.
The Domino Effect Theory of accident causation proposed by HW Heinrich may explain the justification for this.
Preventable injuries culminate from a series of sequential events, as represented by five dominos.
The first represents the task or situation, followed by some faulty
worker decision, resulting in the unsafe action, which leads to an
accident and the inevitable injury.
By tipping the first domino all tend to fall, and by removing some of the intervening dominos the accident can be eliminated.
Hence the belief that workers' decisions or actions are the primary cause of accidents.
The findings of two major research studies supported this conclusion.
The first by Heinrich in 1931 where he analyzed over seventy thousand accidents.
He found that:
- 88 percent of injuries resulted from actions of employees;
- 10 percent of the accidents were traced to hazards involving the physical environment;
- 2 percent of the accident’s cause could not be ascertained.
- The even larger one by FE Bird in 1966 which analyzed over 1.7
million accident reports from hundreds of companies and concluded that:
- 95 percent of injuries resulted from actions of employees;
- 5 percent of the accidents were traced to causes from the physical environment.
These studies confirmed that most accidents were caused by some
action by the worker thereby focusing intervention on changing their
action or behaviors in order to reduce and eliminate accidents.
Beliefs regarding accident causation
Accident causation may be affected by beliefs associated with:
- Individual factors (age, experience, personality, motivation, perception, needs, expectations, etc.),
- Social factors (lifestyle, family issues, education, economic status, etc.)
- Cognitive factors (understanding, reasoning, comprehension, insight, intelligence, etc.)
- Circumstantial factors (perceived work relationship with supervisor or peers, degree of perceived exposure, job security, etc.)
- Organizational factors (e.g., culture, climate, management's attitude, group norms, etc.)
In many industries but especially construction, all people
involved—from the organization’s workers through to executives; and
partners in the supply chain have some understanding of the existence of
worksite risks, but have different opinions as to how this results in
accidents and injuries as well as how to best deal with this reality.
This thinking (belief or bias) fundamentally impacts the way risk
and safety are evaluated, addressed and the effectiveness of preventive
measures devised and deployed.
Supervision factors
The same accident may be attributed to various factors stemming
from different beliefs about accident causation as held by different
people (foremen, superintendents, managers, experts, safety
practitioners, etc.) working on the job site.
Prevailing wisdom attributes the cause of the accident to the decision made or behavior engaged in by the worker.
This may include such things as inattention, inexperience, lack of
focus, rushing, carelessness, fatigue, complacency, ignorance, not using
common sense, failure to follow good work practices, or even downright
stupidity to name a few.
The worker may take risk for convenience, or due to happenstance.
These biases may be motivated or driven by one's belief system,
one's position in the organization, or possible involvement in
causation, to name a few.
This posture and ultimate goal are defensive in nature.
The positions of those involved will become more entrenched and
will be greatly affected by the seriousness of the accident and the
ultimate potential outcome of the situation.
Worker factors
The reasons given for accidents by workers provide a window into
their attitudes and beliefs about safety, accident causation, or the
confidence they have in their ability to deal with hazardous work
situations.
The worker involved in the accident may attribute the cause of the
accident to operational factors, such as the need to rush in order to
meet production goals, maybe the unavailability of proper tools or
equipment or their condition, and a lack of protective measures or
equipment, little or no concern for safety.
On the worker's part, risk taking may be associated with confidence
in their ability to deal with the risks involved due to past
experience, confidence in their skills, underestimating the level of the
risk, or the degree of exposure.
Workers who need the work will generally accept a higher level of
risk, work in environments that are more hazardous, and use tools that
may be inappropriate for the task, in order to meet perceived or actual
expectations.
Or they may simply attribute the accident to bad luck.
Systems factors
Another way to look at the basic Domino Effect Theory is to look at
the first domino (task or environment) and make a determination as to
why the risk existed in the first place and whether it could have been
eliminated or its negative impact diminished; prior to assigning the
task to the worker.
This is probably the most effective approach to eliminating accidents or reducing their adverse effects.
This step involves the person responsible for planning, directing, executing, and/or controlling the work.
The next question involves the second domino and a determination
should be made as to why the worker decided to proceed in the way that
they did which led to the accident and the resulting injury.
This requires understanding whether the worker identified the risk,
was able to determine its significance, the degree of exposure, have
the capability to perform the task, etc.
This requires the appreciation and understanding that systems
(policies, practices, and procedures) may create situations that allow
risk to enter into the work process and may be the primary source of
risk in the work environment.
Conclusion
Beliefs involving the impact of risk on the worker's safety and the
perceived benefit of risk taking should be a factor that is assessed
when considering or evaluating the motivation underlying the resulting
behavior.
Depending on the situation, beliefs can positively or negatively affect safety and its management.
Beliefs about control are important to accident analysis and the explanations of causation.
By gaining insight into such beliefs and taking those into account,
accidents may be analyzed more realistically, and robust preventive
measures can be devised and implemented.
The importance that beliefs play in workplace safety and its management has been identified in numerous research studies.
Researchers have also verified that subjective judgment by people is a major component in any risk assessment.
If such judgment is faulty, the risk management process and efforts
will, in all likelihood, be misdirected and garner inferior or no
beneficial results.
It has been asserted that in reality, much of accident preventive
measures are driven by causal inferences rather than the actual drivers
of such events.