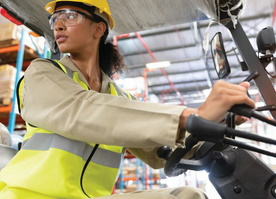
As a safety professional, have you ever faced resistance from
management when you’ve proposed employee safety training initiatives?
Chances are you’ve heard responses like: “We don’t have the time;” “We
don’t have the budget;” or “I need you to condense that eight-hour
training class into three hours.” The fact is training is costly.
Consider the ‘forgetting curve’
On top of the cost objection, according to research, up to 90 per
cent of training is forgotten within seven days. The “forgetting curve”
was hypothesized and tested by German psychologist Hermann Ebbinghaus.
His research showed that when people first learn something, it
disappears at an exponential rate. In fact, most learning is lost in the
first couple of days. However, if we understand how learning occurs,
then we can do something about the forgetting curve and demonstrate to
management with confidence how they can deliver safety training that
produces a return on investment. A key reason for the forgetting curve
is that three parts of the brain are involved in learning retention and
competency, and most training only engages one part of the brain — and
at best two. Knowledge, application and competency reside in different
parts of the brain.
Knowledge: Lets take forklift training, for example. When workers
sit through the lecture, watch the videos, or read the safe work
procedure on how to operate a forklift, neurons fire in the neocortex of
the brain to log the new information by making new synaptic
connections. The neocortex is the seat of our conscious awareness and
where we store information. In 2000, Nobel Prize winner Eric Kandel
found that if information is not reviewed or applied, the new circuits
formed in the neocortex prune apart within hours or days. As the saying
goes: “If you don’t use it, you lose it!”
Application: As they review their workbooks and watch the videos
about how to operate the forklift, workers might be thinking “Hey, I’ve
got this… This looks easy!” However, out in the parking lot when its
time to apply what they have just intellectually learned, they find out
that it’s actually not that easy. The forklift jerks forward, hydraulics
go up when they were meant to go down, and the pallet gets dropped. The
reason for difficulty is because “doing” or application resides in a
different part of the brain — the limbic brain. The application of the
new knowledge (or experience) causes jungles of neurons to organize into
networks and the brain makes a chemical that activates the limbic brain
to releases neuropeptides. Now the workers are beginning to chemically
instruct and emotionally teach their body what the mind has
intellectually understood. So, knowledge is for the mind (neocortex),
but application or experience is for the body (limbic brain).
Competency: After a few weeks or months, the workers are so skilled
at operating the forklift that they don’t have to consciously think
about what they are doing. They can even be talking to another worker in
the area all while scooping and setting a pallet perfectly. They have
applied the knowledge enough times, so that now they no longer have to
consciously think about it. When workers have repeated something over
and over, it causes neural networks in the cerebellum, the storehouse of
implicit (non-declarative) memory, to become highly enriched. Now,
their body as the unconscious mind is operating the forklift, and
neurochemically, mind and body have become as one. So, if learning is
making new synaptic connections in the brain, then remembering is
maintaining and sustaining those connections. Competency, then, is
neuroconnections fired and wired through repeated application so that
the worker can perform the task skillfully with their body as the
unconscious mind — just like tying our shoelace. When we understand how
the brain and body learn, we have a better understanding why the
learning pyramid estimates retention at five to 10 per cent with lecture
or reading alone.
Tips for better training outcomes
1. Make it meaningful: People are more likely to pay attention and
retain information when they are interested in the content, and they
understand how it practically applies to them.
2. Make it interactive: The more participants interact with the
content, the more the brain has to fire and wire, and the better the
learning and retention. For example, if people can turn to the person
next to them end explain what they just learned, they are building a
model of understanding.
3. Promote critical thinking: Build case studies and scenarios into
your training program. As people apply what they have just learned
immediately, the brain starts firing in new patterns, sequences, and
combinations and the new neurosynaptic connections being formed are more
likely to stick. Moreover, questions hook the brain, making people
think. This then causes more neurons to fire and wire to promote
learning and retention.
4. Deliver content in micro-courses: Instead of a full-day training
program, consider breaking it down into three sessions of two hours
each. Learning drops off significantly and even stops when people feel
overloaded or overwhelmed.
5. Include application right away: Make sure people apply what they
are learning. Remember that “experience” resides in a completely
different part of the brain. For example, have students create the WHMIS
workplace label, physically set up the ladder, practice running to get
the AED and calling for help.
6. Test for understanding: Whether it’s a written test or a
competency checklist — or both — it’s another way for the knowledge to
be applied. It also measures the level of learning and provides a record
for your company’s due diligence.
7. Revisit the material often: Send an email, hold a safety talk,
and host short refresher courses often, so that the brain fires and
wires into a long-lasting connection.
In summary, every year, organizations invest billions in
performance-based training that fails to produce the desired results.
Why? A primary reason is the inability to produce the sustained change
required to have a lasting impact on human behavior. True and lasting
change requires becoming aware of how the brain works and creating
deep-seeded habits and beliefs that rest mostly in the unconscious mind.
Next time management pushes back on allocating safety training time
or dollars, share your understanding of how learning occurs to help
assure them why and how they’re going to get a return on their
investment.