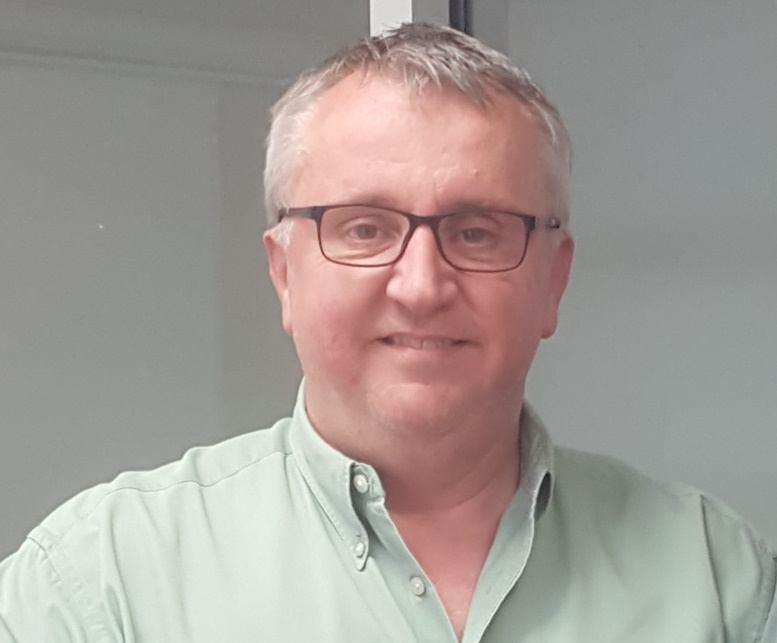
Back in 2016 we celebrated our 35th anniversary and featured a series of tribute articles titled “On the Shoulders of Giants”.
The articles acknowledged five seminal figures in IVES’ history
with “honorable mentions” whose contributions to the company have been
critical in its creation and ongoing success: Susan Ives, Wally Adams,
Don Black, and the subject of this article – current GM, President/CEO
and Head Director of Training Rob Vetter.
Each of the figures provided vital elements to the IVES’ recipe for
success and it is on the shoulders of these giants that the company was
built and still stands today.
This year not only marks the 40th anniversary of IVES, but it is also Rob Vetter’s 25th year with the company on October 16.
We would like to congratulate Rob for this major milestone
achievement and thank him for his constant dedication to the company and
its mission.
There is not enough room on this page to list all of Rob’s contributions to the company over his 25-year tenure.
However, it must be mentioned that he has worked tirelessly to
ensure that IVES training materials continue to evolve and improve the
level of communication required to efficiently and expertly enable IVES
qualified mobile equipment trainers to train and certify competent
operators.
In addition to upgrading our training materials, Rob has also
written many of the featured articles in the IVES Update Newsletter.
No matter the endeavor, Rob always abides by what IVES truly stands
for in all meanings of the word, and for those of you that don’t know:
IVES stands for Integrity, Value, Expertise, and Support.
When asked what it is like to work with Rob, IVES' Operations
Manager Ron Shankar replied “I have learned many valuable lessons from
Rob, not only about business but also about how to live my best life.
Rob is very humble, and I must take this opportunity to mention
that although Rob may seem to have a quiet demeanor, his brain is like a
super-computer and business acumen seems to just come naturally to him.
Rob can process information effectively and quickly to make
business decisions. If I had to choose one word to describe how Rob
conducts himself in business, I would use the word ‘Integrity’.
Whether he is formulating the company’s business practices, or
crafting the technical information referenced in IVES training
materials, Rob will never compromise the integrity of this company.
This is something he puts first and foremost above all else in his business dealings."
Rob must be considered one of the seminal figures in IVES’ history
whose contributions to the company have been (and continue to be)
critical in its continuing success and therefore, he is no longer just
an “honorable mention”.