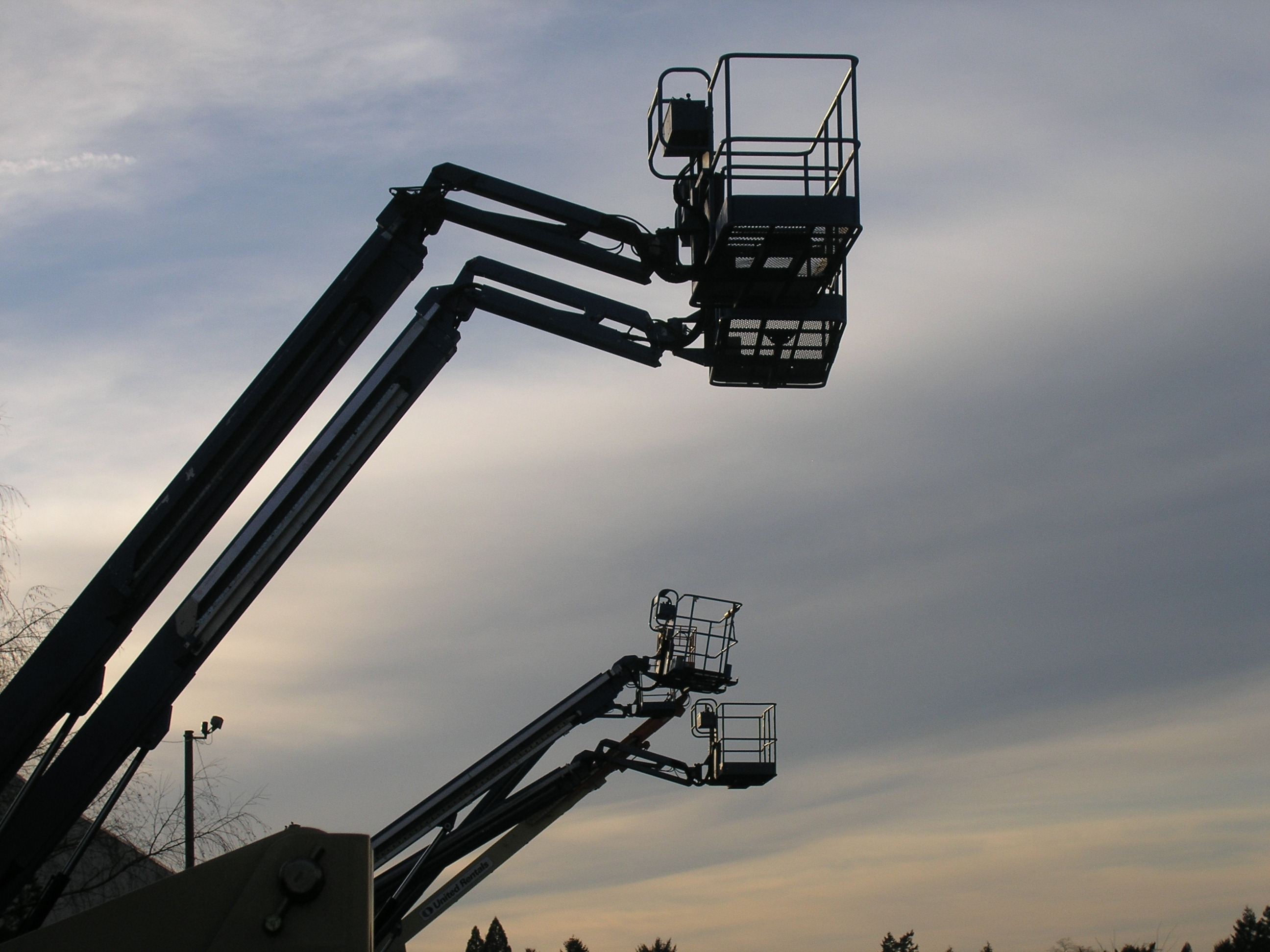
There is no argument to the fact that work must be performed at height.
Some people think of aerial lifts as being a sophisticated piece of
equipment exclusive to the construction industry. This could not be
farther from the truth.
Trade workers, photographers, small business owners, filmmakers,
and others utilize mobile elevating work platforms (MEWPs) to enhance
their business.
So, what brought about the need for the access industry to
re-evaluate the traditional chain so common on 3a or 3a+ vertical
scissor lifts? Injury of course!
Falls are and have been for nearly a decade the number one cause of
injury and death, not just in America but across the global
construction industry. Scissor lifts do not have the same requirements
for fall protection that 3b or 3b+ articulating/straight booms have.
The reasons for that distinction in fall protection requirements
comes down to a deeper understanding of the hazards associated to both
classes of equipment.
Some MEWPs require personal fall protection equipment, and some do
not. The access industry has realized that the weakest link in their
chain of safety was the chain at the entry gate!
Two Groups of Fall Protection
Understanding the terminology is important when making decisions
about a rental or purchase. There are two groups of fall protection,
active and passive.
• Active fall protection = Dynamic systems that contain moving parts.
- Restraint – Prevented from reaching an area of risk, restrained from the edge.
- Positioning – Positioned securely through tension or suspension in an area of risk.
- Arrest – Prepared by utilization of fall protection systems (FPS) that only limit the impact force in an area of risk.
• Passive fall protection = Non-dynamic systems that are stationary.
- Stair rails and guardrails – Prevent a fall through permanent installation.
- Barricades and scaffolding – Positioned temporary systems.
- Safety netting – Prepared to absorb and contain.
Based on this terminology, the entry gate is a form of passive fall
protection that allows prevention of falls like a restraint system with
active fall protection methods. Not many people looked at passive
protection in this light. However, it was this innate understanding that
led to the change.
In early 2000, members of the European Committee for
Standardization (CEN) EN280 Committee desired to increase the safe use
of elevated work platforms.
In 2009, CEN published new rule making for MEWPs, including design
calculations, stability criteria, construction, safety, examinations,
and tests (citation: prEN 280:2009 (E), CEN/TC 98 2009-02). That is when
the first change came about.
The rule was clear: “Chains or ropes shall not be used as guard-rails or access gates. Verification – by visual examination.”
The American National Standards Institute (ANSI) was soon to
follow. Work began and discussion led to the creation of 10 sections
within a new suite of standards specific to the same issue. Employers
and users of aerial equipment designed to comply to ANSI/Scaffold &
Access Industry Association (SAIA) A92.20-2020, however, are not
required to retroactively make changes to equipment manufactured before
June 1, 2020, the effective date of the standard.
What You Need to Know!
- Access entry points must have a toe-board.
- Swing gates will be much more common.
What Does the ANSI/SAIA A92.20 Standard Say?
- 4.6.6.1 Any opening in the floor or between the floor and toe
guards or access gates shall be dimensioned to prevent the passage of a
sphere of 15 mm (.59 in) diameter. 4.6.7 Chains or ropes shall not be
used as guardrails or access gates.
- 4.6.7 Chains or ropes shall not be used as guardrails or access
gates. A popular solution for manufacturers has been a fixed bar across
the top of the aft end of the rails with a half gate that opens on the
bottom. This solution can be seen on scissor lifts with folding rails.
So be on the lookout going forward. Dayby-day, saloon-style gates
and cantilevers entries will be much more prevalent than chains.
Being informed is key. Understanding that the new standards are not
retroactive will give insight into how to handle a machine that arrives
on your jobsite.
The aftermarket industry is full of resources by the original
equipment manufacturing (OEM) community to provide ways to use older
machines safely.
To learn more, be sure to purchase and review the most recent
ANSI/SAIA standards and to have on hand the SAIA Manual of
Responsibilities.
Give your partner in safety a call and join the SAIA at its 2021
Annual Convention & Exposition to be introduced to a room full of
passionate SAIA members.